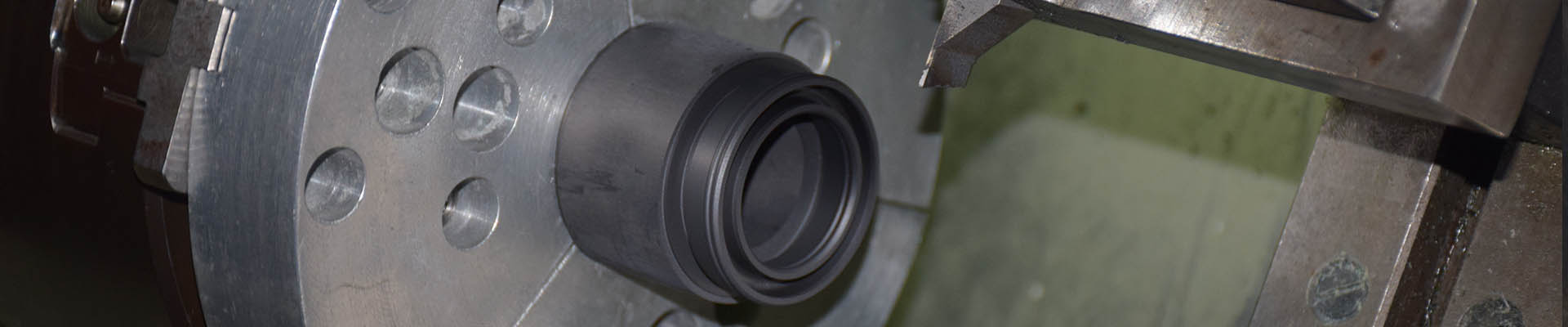
How can FFKM improve the oil& gas ESP's reliability?
When it comes to sealing in harsh operating conditions, the Upstream Oil & Gas industry has some of the toughest applications out there. With fluids such as hydrocarbons and gases such as H2S, combined with pressures climbing well above 20k psi and temperatures drifting to 200° C and higher, reliability in sealing is an absolute must to mitigate against unproductive downtime. Adding steam and amine-based corrosion inhibitors to this mixture provides additional complexity to material selection in a downhole environment.
A variety of elastomeric materials are available for sealing downhole, however, perfluoroelastomers (FFKM) provide the highest temperature capability and broadest chemical resistance of any rubber material. Over the lifetime of an application, FFKMs supply excellent total cost of ownership by minimizing equipment downtime due to greater reliability in elevated temperatures and corrosive fluid conditions. As oilfield technology evolves to gain more efficiencies and optimize production, sealing technology also needs to evolve.
In a recent example, JST put its application expertise to use when examining what it would take to extend the life of a critical component like an electrical submersible pump (ESP) in SAG-D wells. Application data showed that ESPs typically operate between 135° C and 220° C with maximum operating temperatures around 250° C. Internal analysis of publicly reported data1 showed that combining operational improvements with upgraded critical components such as seals to materials with high temperature resistance such as FFKM can decrease the risk of premature failure. By extending the ESP’s lifetime, operators may avoid non-productive downtime and the expense of pulling an ESP out of a well ahead of scheduled maintenance.
After analyzing data and key failure modes, JST collected customer feedback that supported the hypothesis that high temperatures combined with steam decreased the lifetime of existing sealing solutions in SAG-D wells. These findings showed that that to improve reliability in SAG-D applications, a next generation sealing solution combining broad chemical resistance to typical Oilfield chemicals and fluids and better physical property retention after steam aging was required.
Collaborating with our customers, we established acceptable property retention for a new compound after an aggressive steam aged test of 1 week at 260°C. This compound exhibited retention of tensile strength, tensile elongation, and modulus of less than 30 percent maximum loss in addition to low hardness and volume change. We established a benchmark FFKM compound known for its steam resistance and high temperature capability. The benchmark tests showed that this compound lost over 50 percent tensile strength and modulus after the 1-week steam aging test using AS568-214 O-rings even though it experienced low hardness and volume change after the steam aging test.
The next steps in the development process involved evaluating FFKM base polymers from four different suppliers, vetting available FFKM cure systems, and then evaluating over 20 different filler packages to obtain consistently passing scores on the steam aging test. We then ran the long term (1000 hour) compression set tests as outlined above and calculated the temperature at which AS568A-214 O-Rings would reach 80 percent compression set in air for 1000 hours at 258°C. Compression set, which measures the deformation of material over time and temperature, can give a good indication of what the lifetime of a particular material is at given temperature. Multiple formulations were tested and adjusted until we reached the required compression set that showed improvement over the control compound.
The extensive research and development process concluded with the final optimization of the formulation that was then commercialized for use at FFKM. Extensive testing demonstrated that FFKM outperformed competitor materials after an extended time at 260°C in steam and short-term exposure to a peak excursion at 316˚C. Other comprehensive testing regimes carried out under a variety of conditions have shown FFKM as the “Go-To” solution to increasing reliability of equipment in critical high temperature steam environments, including SAG-D.
New Blog
© Copyright: 2025 Guangzhou JST Seals Technology Co., Ltd. All Rights Reserved.
Scan to wechat