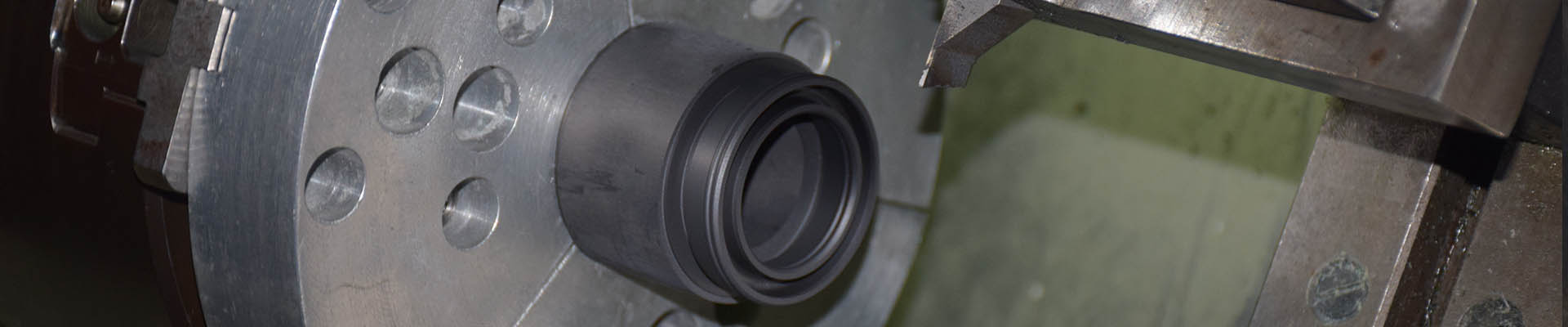
What are the factors that cause seal leakage and How to solve them?
Seal leakage of equipment in the oil, natural gas, and chemical industries would cause great loss of production, and it would cause severe environmental pollution, which has gradually increased users' requirements for safety sealing solutions.
There are many factors that can cause seal leakage, the more common ones are as follows:
1. Installation problems:
a. Wrong installation direction of the seal leads to leakage;
b. Foreign matter or dust mixed in or in the pipeline during installation enter the seal and cause leakage;
c. Poor assembly causes seal damage and leakage;
d. Scratches on the surface of the sealing rod cause leakage;
e. Insufficient concentricity during welding process leads to eccentricity, and eccentric load causes leakage;
f. Uneven coating processing, paint enters the sealing ring.
2. Seal selection problems
a. Gap bite caused by excessive pressure;
b. After mixing with air, adiabatic compression causes seal burnout;
c. The sealing material is incompatible with the medium, causing material deterioration such as expansion and reflection;
d. The material deterioration caused by high temperature;
e. The low temperature causes the material to harden, shrink and cause leakage;
f. High-frequency reciprocating motion causes the seal to heat up and dry grinding;
g. At low pressure and low speed, the movement is not stable;
h. Poor lubrication leads to seal wear increased;
i. Leakage caused by vibration of components;
j. Abnormal wear of the seal ring caused by environmental dust;
k. The rust of the sealing groove causes leakage.
3. Sealing assembly design issues
a. Inappropriate selection of the material of the guide support will damage the cylinder tube and piston rod;
b. The gap of the friction pair is not suitable, causing the gap to squeeze out and bite;
c. Improper lead angle of the thread at the end of the cylinder, piston and cylinder, damages the sealing ring;
d. Stiffness and weight calculation errors cause poor movement;
e. Improper sealing installation angle leads to the damages to the sealing ring;
f. The roughness of the sliding surface is not suitable, causing the wear of the sealing ring;
g. The electroplating is uneven, and the sealing ring may be scratched or worn on the surface through which the seal is passed;
h. The sealing groove, especially the shaft sealing groove roughness is not enough, causing the wear of the sealing ring and damage the seal;
i. Piston, piston rod coating pores cause leakage;
j. Poor lubrication and wear, bite the cylinder and piston rod.
4. Storage issues
a. Due to the high temperature during storage and transportation it will cause the deterioration of the sealing material;
b. Strong sunlight, ozone, and radiation cause deterioration of the sealing material;
c. Lack of proper preservation methods, deforming the sealing ring;
d. Long-term storage will cause the sealing material to age.
How to solve above mentioned issues?
First of all, the use of good quality seals can greatly help users reduce the risk of leakage. Make sure the material selection meet the application conditions. Also the product usually has a bright and clean appearance without adhesion, bubbles, and burrs. There is no shortage of material or breakage in the quality, and the size should also meet the standards and user needs.
When installing the seal, first check that the groove is clean and free of debris. After the inspection, the outer surface of the seal should be coated with appropriate lubricant, and the lip should be coated with appropriate clean grease. For seals with dust lip, fill the space between the primary and secondary lips with suitable clean grease before assembling. Turn the sealing lip end of the seal toward the side of the sealing medium, and avoid reverse assembly. When the seal is installed in the seat hole, it should be pushed in with a special tool to prevent the position from deviating. Various measures should be taken to prevent damage to the lip at the thread, keyway, spline, etc. through which the lip of the seal passes, and special tools should be used for assembly. The seal should be placed horizontally in the seat hole and pressurized evenly, do not force it to tilt.
The quality of the sealing effect plays an important role in the reliable operation of the application equipment system, ensuring the precision of the design, and adopting the correct assembly method to assemble the equipment. The seal is not easy to be damaged, the elasticity is good, and the service life is long, which is conducive to improving the product, the quality and sealing performance.
Previous :
What is O Ring?Next :
What are Spring Energized Seals?New Blog
© Copyright: 2025 Guangzhou JST Seals Technology Co., Ltd. All Rights Reserved.
Scan to wechat