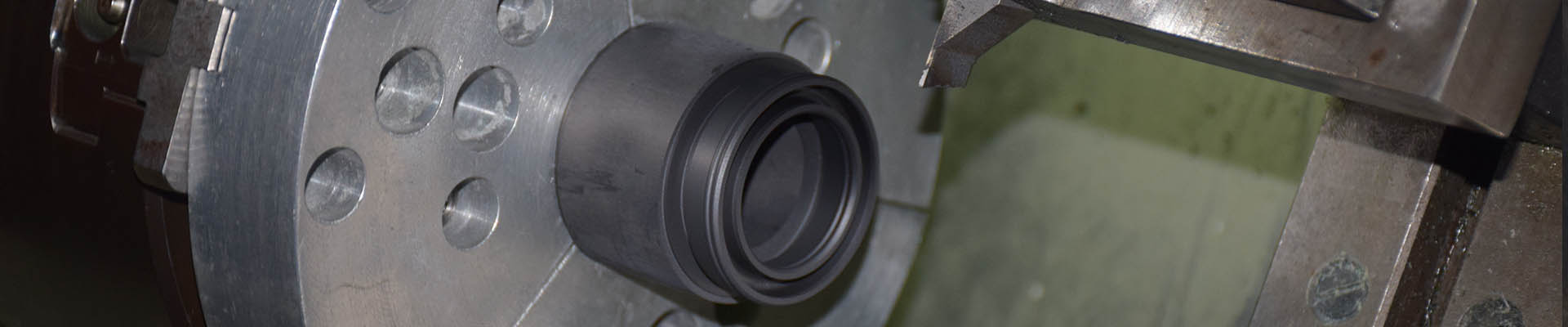
What is the Right Surface Finish for Your Seal's Mating Hardware?
If the sealing system on your equipment fails prematurely or cannot work normally, you may immediately check the following points:
Whether the seal is defective;
Whether the sealing material can not withstand the temperature or pressure requirements of the application;
Whether the size is appropriate or the extrusion level is verified;
However, the inspection of mating metal components is easy to be ignored. Some aspects of the hardware design may affect or damage the ability of the seals to operate normally, and may affect the dynamic life of the sealing elements. The surface finish of the mating metal components (the roughness of the two hardware surfaces of the compression seal) is one of the factors that should be considered in the design, because the ideal surface finish will determine the sealing performance and can maximize the service life of the sealing elements.
The surface finish requirements depend on whether the seals are elastomer, thermoplastic or other materials. The overall ductility of the elastomer makes the surface finish have greater consistency, while the consistency of the rigid thermoplastic is lower, but due to its tribological characteristics, it may sometimes require less lubrication. Therefore, it is recommended that the surface finish of thermoplastic seals is generally higher than that of elastomer seals.
In addition, the surface finish requirements for sealing liquid applications are different from those for sealing gas or vacuum applications. For gas seals or vacuum seals, it is recommended to use a higher surface finish, because the structure and size of most gases allow them to pass through smaller gaps than liquids.
In dynamic applications, the surface finish of metal components will also directly affect the service life of seals. Changes in the surface of metal components require the retention of process media or lubricants on the surface to reduce friction. However, if the surface is too rough, the sealing element will be worn due to movement on the metal components. It will also be difficult to adapt to all changes in local surface height. Intercept process medium or lubricant, and reduce friction through continuous dynamic circulation. Therefore, it is very important to find the right balance to provide lubrication and maximize the seal life.
New Blog
© Copyright: 2025 Guangzhou JST Seals Technology Co., Ltd. All Rights Reserved.
Scan to wechat